Once again, tackling a well known topic, I risk to sound ridiculous but hold your judgement till you have some material objections to make. Jumping ahead I will say, that the issue of "we did not build this ship" extends way beyond these three ships. In reality, this is one of those instances, where I would like this community to find a conventional explanation for the question I will pose. In other words, I would love to be proved wrong on this one, for we have videos, photos, blueprints, and what not.
The question I will pose is this - what did they use to connect 2.5 ton hull plates to each other? Rivets, invisible rivets, welding or glue?
There was a lot published about RMS Titanic and its two sisters, RMS Olympic and HMHS Britannic. For those who do not know, or their knowledge is superficial, below is a little recap.
The White Star Line faced an increasing challenge from its main rivals Cunard, which had recently launched the Lusitania and the Mauretania - the fastest passenger ships then in service - and the German lines Hamburg America and Norddeutscher Lloyd. The company sought an upgrade in their fleet primarily in response to the Cunard giants but also to replace their oldest pair of passenger ships still in service, being the SS Teutonic of 1889 and SS Majestic of 1890. All three Olympic-class liners were built by Harland and Wolff (Belfast). The plan to build these three ships was realized by naval architects Thomas Andrews and Alexander Carlisle.
Alexander Carlisle got off the project in 1910 due to health problems. Thomas Andrews died on Titanic when she hit an iceberg on 14 April 1912. His body was never recovered.
Although Olympic and Titanic were nearly identical, and were based on the same core design, a few alterations were made to Titanic (and later on Britannic) based on experience gained from Olympic's first year in service. The most noticeable of these was that the forward half of Titanic's A Deck promenade was enclosed by a steel screen with sliding windows, to provide additional shelter, whereas Olympic's promenade deck remained open along its whole length. This was a major contributor to Titanic's increased gross tonnage of 46,328 tons over Olympic's 45,324 tons, which allowed Titanic to claim the title of largest ship in the world.
Titanic was 882 feet 9 inches (269.06 m) long with a maximum breadth of 92 feet 6 inches (28.19 m). Her total height, measured from the base of the keel to the top of the bridge, was 104 feet (32 m). She measured 46,328 gross register tons and with a draught of 34 feet 7 inches (10.54 m), she displaced 52,310 tons.
HMHS Britannic
The dimensions of Britannic were similar to those of her sister ships, but her dimensions were altered whilst still on the building stocks after the Titanic disaster. With a gross tonnage of 48,158, she surpassed her sisters in terms of size (volume), but that did not make her the largest passenger ship in service at that time; the German SS Vaterland was significantly bigger.
In reality, we only have a few stages of the construction of RMS Titanic. They are:
With all the video, and photographic evidence we have where is the Titanic, or Olympic or Britannic at the stage where their hulls are 1/8, 1/4, 1/2 complete? How did they attach those bottom 2.5-3 tons, 6 foot by 300 foot still plates? Did they weld them together, or did they glue them together? And why did they have to use rivets above the unriveted portion?
After all, how invisible can iron rivets be?
Olympic propeller shot. This is a huge image you can zoom in on. You will find a few rivets in there, closer to the rudder. The remainder is mystery.
It gets better. Where are the rivets on this 1856 ship:
Here is a 28.6 MB TIFF image link to a huge image of this ship. If you can find a rivet here, I would like to hear about it. What you will find there is a few of the seams looking just like welding seams look.
Finding close enough images of those early 20th century "high-tech marvels of their time" is hard. But they are out there, and sometimes they pose questions. There are multiple videos out there which show ships being built, like this one of supposedly RMS Olympic... or it could be 1930 RMS Queen Mary, or any other ship for that matter. Those videos show something and nothing.
I present a simple question, if rivets were not used, and welding was not available around 1912 (definitely was not in 1856 for SS Great Eastern), how were those plates attached to each other in the unriveted areas? Superglue was invented in 1942, so they could not use that.
Additionally, you will not find a name attached to the invention of a VPP (variable pitch propeller). General Wiki link on propellers is here. All three of our Olympic-class ships had 2 Variable pitch propellers, and 1 Fixed Pitch Propeller. I talked about the difference between the VPP and FPP in the article about SS Great Eastern. In a nutshell the below two images show the difference between VPP and FPP.
Now think about it.
KD Hypothesis: Starting with the mid-19th Century, and ending with approximately 1917-1920s, Britain, and Germany (possibly USA, and France as well) acquired (through military involvement) a number of the Tartarian Ships of superior quality. The Grand Tartary was obviously destroyed, and wiped out from history. Not being able to use the ships the way they were (military induced damage, or technological mismatch - Titanic's electrical plant was capable of producing more power than an average city power station of the time), the victors (or the survivors, or vultures) had to repair, refurbish, and adjust them to their technological level (coal fuel, etc). For that purpose dry docks were constructed. Captured ships were adjusted in those docks. Ships originally had no funnels, due to different "cleaner" fuel used to power their steam engines. Funnels were installed to accommodate hundreds of tons of ash emitted by the readjusted engines.
Poor understanding of the acquired machinery meant multiple operational errors, and consequent short life span of these ships. That is unless ship welding was available in 1856, and 1912. Otherwise what did they use to hold those plates together - invisible rivets? Super strong glue could also be an option, I guess.
That is unless ship welding was available in 1856, and 1912. Otherwise what did they use to hold those plates together - invisible rivets? Super strong glue could also be an option, I guess.
The question I will pose is this - what did they use to connect 2.5 ton hull plates to each other? Rivets, invisible rivets, welding or glue?
There was a lot published about RMS Titanic and its two sisters, RMS Olympic and HMHS Britannic. For those who do not know, or their knowledge is superficial, below is a little recap.
The White Star Line faced an increasing challenge from its main rivals Cunard, which had recently launched the Lusitania and the Mauretania - the fastest passenger ships then in service - and the German lines Hamburg America and Norddeutscher Lloyd. The company sought an upgrade in their fleet primarily in response to the Cunard giants but also to replace their oldest pair of passenger ships still in service, being the SS Teutonic of 1889 and SS Majestic of 1890. All three Olympic-class liners were built by Harland and Wolff (Belfast). The plan to build these three ships was realized by naval architects Thomas Andrews and Alexander Carlisle.
RMS Olympic
Although Olympic and Titanic were nearly identical, and were based on the same core design, a few alterations were made to Titanic (and later on Britannic) based on experience gained from Olympic's first year in service. The most noticeable of these was that the forward half of Titanic's A Deck promenade was enclosed by a steel screen with sliding windows, to provide additional shelter, whereas Olympic's promenade deck remained open along its whole length. This was a major contributor to Titanic's increased gross tonnage of 46,328 tons over Olympic's 45,324 tons, which allowed Titanic to claim the title of largest ship in the world.
- Laid down: 16 December 1908
- Launched: 20 October 1910
- Completed: 31 May 1911
- In Service: 1911
- Out of Service: 1935
- Hull plates held by: 3,000,000+ rivets
- Fate: Retired at Southampton after 24 years service & scrapped. Superstructure dismantled at Jarrow, England, and the hull at Inverkeithing, Scotland.
- Wiki link
RMS Titanic
Titanic was 882 feet 9 inches (269.06 m) long with a maximum breadth of 92 feet 6 inches (28.19 m). Her total height, measured from the base of the keel to the top of the bridge, was 104 feet (32 m). She measured 46,328 gross register tons and with a draught of 34 feet 7 inches (10.54 m), she displaced 52,310 tons.
- Laid down: 31 March 1909
- Launched: 31 May 1911
- Completed: 2 April 1912
- In Service: 10 April 1912
- Out of Service: 15 April 1912
- 2,000 Hull plates held by: 3,000,000+ rivets
- Fate: Hit an iceberg 11:40 p.m. (ship's time) 14 April 1912 on her maiden voyage and sank 2 h 40 min later on 15 April 1912.
- Wiki link
In other words, they did not use welding to put hulls together back in 1912 (or 1913, 14, 15, or 16).The 2,000 hull plates were single pieces of rolled steel plate, mostly up to 6 feet (1.8 m) wide and 30 feet (9.1 m) long and weighing between 2.5 and 3 tons. Commercial oxy-fuel and electric arc welding methods, ubiquitous in fabrication today, were still in their infancy; like most other iron and steel structures of the era, the hull was held together with over three million iron and steel rivets, which by themselves weighed over 1,200 tons. They were fitted using hydraulic machines or were hammered in by hand.
HMHS Britannic
The dimensions of Britannic were similar to those of her sister ships, but her dimensions were altered whilst still on the building stocks after the Titanic disaster. With a gross tonnage of 48,158, she surpassed her sisters in terms of size (volume), but that did not make her the largest passenger ship in service at that time; the German SS Vaterland was significantly bigger.
- Laid down: 30 November 1911
- Launched: 26 February 1914
- Completed: 12 December 1915
- In Service: 23 December 1915
- Out of Service: 21 November 1916
- Fate: Sank after an explosion on 21 November 1916 near Kea in the Aegean Sea
- Wiki link
USS Northland
USS Northland was a cruising class of gunboat especially designed for Arctic operations that served in World War II and later served in the Israeli Navy. She was the last cruising cutter built for the Coast Guard equipped with a sailing rig.
- Laid down: 26 August 1926
- Launched: 5 February 1927
- Commissioned: 7 May 1927
- Out of Service: 1938–1939
- Fate: Sold 3 January 1947
- Wiki link
Essentially, USS Northland was one of the first officially welded ships. You are welcome to find an earlier one, and I will gladly update this post with your finding.She was structurally reinforced to withstand hull pressures of 100 psi and lined with cork for warmth. One feature used in the construction was the welding of the hull rather than riveting; this was done for strength and was not a common practice in 1926.
To speed up and improve production, shipyards started using templates to manufacture prefabricated ships and replacing riveting with welding. The 2,710 cargo ships they built between 1941 and 1945 were called “Liberty Ships.” They were credited with helping to win the war.
Construction of Titanic
RSM Titanic is obviously the most publicized ship out of the three. Apart from its ill fate and the beautiful name, it is open for speculation why the most videos and photos pertain to Titanic, and not Olympic, for the latter was the first one to get launched. One way or the other, we have plenty of photos and YouTube videos of Titanic being built... or do we?In reality, we only have a few stages of the construction of RMS Titanic. They are:
- Keel Laying
- Construction of the Frames
- Construction of the Hull
- 35 photos of the construction of the Titanic that we don’t often see
- Titanic: Building the largest moving object in history
- Construction of the Titanic: keel, frames, hull
- Rare photos of the construction of the Titanic
- Construction of the Titanic
- YouTube: Titanic Construction
Where are the Rivets?
Images Source
Rivets are very much visible, and distinguishable.
Titanic Hull Rivets
The 401 Rivet is 3 3/4″ long, with a shank diameter of 1″ and head diameter of 1 3/4″. Each one weighs just over 1 pound.
Titanic. Ship Number. 401. Vessel Type. Passenger Ship. Built. Belfast. Yard. North Yard.
Rivets dot the surface of the "Big Piece," the largest recovered section of the Titanic's hull. The 15-ton section of the doomed luxury liner is part of a touring display of more than 300 relics from the ship called "Titanic"Images Source
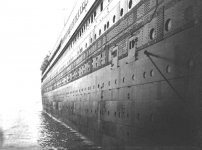
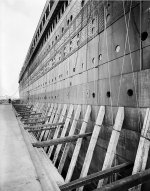
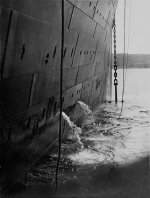
Rivets are very much visible, and distinguishable.
Titanic Hull Rivets
The 401 Rivet is 3 3/4″ long, with a shank diameter of 1″ and head diameter of 1 3/4″. Each one weighs just over 1 pound.
Titanic. Ship Number. 401. Vessel Type. Passenger Ship. Built. Belfast. Yard. North Yard.
With all the video, and photographic evidence we have where is the Titanic, or Olympic or Britannic at the stage where their hulls are 1/8, 1/4, 1/2 complete? How did they attach those bottom 2.5-3 tons, 6 foot by 300 foot still plates? Did they weld them together, or did they glue them together? And why did they have to use rivets above the unriveted portion?
Flush Rivets
There is an interesting couple of paragraphs in the 1868 book titled "Iron Ship-building, with Practical Illustrations". It could almost solve the mystery if it was not for the lack of evidence of such an "invisible" flush rivet. If you can find what this particular rivet looks like, please post a link, or upload a picture. Also, if you can find any mentioning of the flush rivets in the Titanic's, or any other ships construction, please share your finding. For right now, the only official rivets are the ones displayed above. Below you can see two pages covering these "flush rivets".After all, how invisible can iron rivets be?
Olympic propeller shot. This is a huge image you can zoom in on. You will find a few rivets in there, closer to the rudder. The remainder is mystery.
It gets better. Where are the rivets on this 1856 ship:
Here is a 28.6 MB TIFF image link to a huge image of this ship. If you can find a rivet here, I would like to hear about it. What you will find there is a few of the seams looking just like welding seams look.
Finding close enough images of those early 20th century "high-tech marvels of their time" is hard. But they are out there, and sometimes they pose questions. There are multiple videos out there which show ships being built, like this one of supposedly RMS Olympic... or it could be 1930 RMS Queen Mary, or any other ship for that matter. Those videos show something and nothing.
Weird Stuff
We do have a few contradicting images showing both, rivets and no rivets like these two images of the RMS Olympic propeller area. One clearly shows the lack of the rivets, the other one shows rivets present. What can this inconsistency tell us? The rivets on the first image are visible from 10 miles away. The second image has a few rivets closer to the rudder, but no other ones are visible.I present a simple question, if rivets were not used, and welding was not available around 1912 (definitely was not in 1856 for SS Great Eastern), how were those plates attached to each other in the unriveted areas? Superglue was invented in 1942, so they could not use that.
Additionally, you will not find a name attached to the invention of a VPP (variable pitch propeller). General Wiki link on propellers is here. All three of our Olympic-class ships had 2 Variable pitch propellers, and 1 Fixed Pitch Propeller. I talked about the difference between the VPP and FPP in the article about SS Great Eastern. In a nutshell the below two images show the difference between VPP and FPP.
- Variable Pitch Propeller - the blades rotate via a complex mechanism inside the hub.
- Fixed Pitch Propeller - the blades are permanently attached (welded if you will) to the hub.
- Telegraph inventor: Samuel Morse
- Radio inventor: Guglielmo Marconi (Popov if you want)
- Telephone inventor: Bell and Meucci
- Light Bulb inventor: Edison
- This, and that, and all of the above inventor: Tesla
- Variable Pitch Propeller inventor: WHO?
- Looks like we were able to figure this one out, but it is not looking good for the official history.
Interiors
Interiors were worthy of the "Tartarian" architecture (for those who knows of what I am talking about).KD Hypothesis: Starting with the mid-19th Century, and ending with approximately 1917-1920s, Britain, and Germany (possibly USA, and France as well) acquired (through military involvement) a number of the Tartarian Ships of superior quality. The Grand Tartary was obviously destroyed, and wiped out from history. Not being able to use the ships the way they were (military induced damage, or technological mismatch - Titanic's electrical plant was capable of producing more power than an average city power station of the time), the victors (or the survivors, or vultures) had to repair, refurbish, and adjust them to their technological level (coal fuel, etc). For that purpose dry docks were constructed. Captured ships were adjusted in those docks. Ships originally had no funnels, due to different "cleaner" fuel used to power their steam engines. Funnels were installed to accommodate hundreds of tons of ash emitted by the readjusted engines.
That is unless ship welding was available in 1856, and 1912. Otherwise what did they use to hold those plates together - invisible rivets? Super strong glue could also be an option, I guess.